Remanufacturing has become a topic of interest in the manufacturing world, especially in the electronics industry, and for good reason. While electronics manufacturers have always handled high variation and frequent product upgrades, it is especially true today. Now, it isn’t only a challenge of keeping up with production (changing processes but using similar—if not the same—parts to create new products), but also reducing waste as much as possible to meet business sustainability goals.
Remanufacturing electronics is a great solution for meeting sustainability goals, overcoming component shortages, and saving costs. But, it has to be done right. Understanding the full process of electronics remanufacturing, its benefits and its challenges, can be the difference between losing out on immense economic gains and developing the next sustainability revolution.
What is Electronics Remanufacturing?
Remanufacturing isn’t the same as recycling or refurbishing, nor is it about repairing a product to keep it going. It’s about reusing components of an existing product to create a new product with a full warranty, to be sold as new or remanufactured.
Remanufacturing is an OEM practice that extends the life of electronic components. When completed under the right conditions, remanufacturing within the electronics industry produces components or products that are considered to be the functional equivalent to a new component or product. With the right expertise and tools, they’re indistinguishable from new parts. That’s why the U.S. Federal Trade Commission requires that these parts are labeled as “rebuilt” to distinguish them from new.
Examples of remanufactured components in the electronics industry include:
- Battery remanufacturing
- Remanufactured phones
- Remanufactured laptops and computers
- Remanufactured printed circuit boards (PCBs)
- Remanufactured AC and DC drives
- Remanufactured I/O modules
- Remanufactured programmable logic controllers (PLCs)
- Remanufactured power supplies
- Remanufactured servo controllers
The Benefits of Remanufacturing Electronics
![Manufacturer analyzing electronics for usability in remanufacturing]()
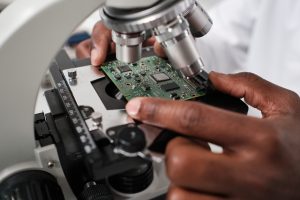
Remanufacturing may be the largest untapped resource for productivity improvement. Some of the largest remanufacturers, including General Electric, Boeing, Caterpillar, Deere, Navistar, Xerox and Pitney Bowes, have built a business model around remanufactured goods. As far back as 2003, these companies were leasing, remanufacturing, and remarketing an estimated $130 billion of assets.
The reasons why remanufacturing remains untapped can be attributed to a lack of awareness of its potential benefits.
Resilience Against Component Shortages
We’re all painfully aware of the chip shortage. While electronics manufacturers can find it challenging to produce new parts at the rate that’s needed, remanufacturing will help get more life out of what we already have. And, given the fast pace of product updates, electronics manufacturers can remanufacture parts from old products and put them into new ones, reducing waste and warding off long lead times as companies wait for parts to arrive to finish a build.
Remanufacturing Saves Money
It’s expensive to replace a faulty product, especially when a few repairs can fix it. By remanufacturing well-functioning components within the whole, electronics manufacturers can save real money. They can gain a like-new product rather than a repaired one, potentially extending the life of the product. On the consumer side, customers can also save money by having the opportunity to purchase remanufactured products at a lower cost—typically 30-40% less than new products.
Testing and Verification
Failing components are like a canary in a coal mine. When one fails, others are likely to go soon. Remanufacturing helps get a fix on the issue and identify the root cause. As remanufacturing requires a full disassembly of a part and assessment of its components, remanufacturers gain insight into what went wrong. Then, manufacturers know where to direct their focus for the next generation of products.
E-waste Reduction
According to the EPA, e-waste is the fastest growing waste stream in the world, fueled primarily by increased consumption of electrical and electronic equipment, shorter product life spans, and few repair options.
Even though 20-50 million metric tons of e-waste are disposed of each year, electronic waste represents only about 2% of all landfill waste. But it accounts for more than 70% of all toxic waste. A large part of what is considered e-waste is whole electronic equipment or parts that can be reused. By remanufacturing components instead of replacing them, less toxic waste is produced. By reducing e-waste through remanufacturing, businesses excel towards a higher level of social responsibility—a factor that may resonate with your customers and shape their perception of your company.
The Challenges of Remanufacturing Electronic
![Manufacturer repairing and soldering the motherboard of a computer]()
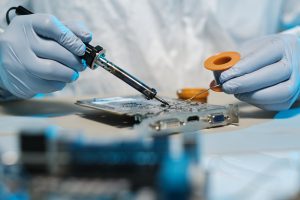
The benefits of remanufacturing are compelling, but to be successful in remanufacturing, it’s important that companies are aware of potential challenges.
Product, Inventory, and Lead Time Management
While remanufacturing provides some resilience against component shortages, it’s hard to guarantee it will fulfill all production needs. For example, you may be able to remanufacture hundreds of printed circuit boards, but you could have thousands of laptops that need them. Then, remanufacturers may have a long lead time as they wait for the right parts to come in to be remanufactured.
Product Variability
Remanufacturing works well for upgrading products within a brand’s product lineup, but many brands use proprietary components. For example, remanufacturing a battery from an iPhone is likely not to fit into a Samsung phone. Even if the battery is the same size, the output may be different or even the placement of the connectors.
Training
Remanufacturing is a complex process. It takes a lot of skill and the ability to understand a wide range of products. So, it can be difficult to find workers with a high-tech background that are also experienced in high variation. The high-variation also restrains remanufacturers from creating standardized training programs, causing them to rely heavily on the knowledge and skill levels of their workers.
Remanufacturing the Future using Augmented Reality
Thankfully, there is technology out there that is proven to streamline and standardize the most complex processes. Augmented reality can seamlessly load the correct disassembly or testing instructions for high variation processes. This high-tech assistance can speed up the disassembly process, giving electronics manufacturers the ability to test and validate parts at a fast pace. Augmented reality assistance in manufacturing also reduces the need for operators to memorize the steps for each variation, making training easier.
Manage the Complexity of Electronics Remanufacturing with Confidence
Remanufacturing has a lot of promise for electronics manufacturers who make a commitment to the process. But it also presents challenges that not every company is prepared to navigate. But with the right tools, it’s possible to reap the economic, social responsibility, and sustainability goals of your business.
Interested in learning how electronics companies are using AR to enhance manufacturing and remanufacturing? Contact us to schedule a consultation with our AR experts.