How to Unlock Insights from Manual Process Data to Improve Manufacturing Analytics
In today’s manufacturing landscape, data is the driving force behind operational transformation. From predictive maintenance and AI-driven insights to IIoT connectivity, companies rely on manufacturing analytics to streamline production and achieve greater efficiency.
Despite advancements in automation and manufacturing analytics, manual workflows often remain a blind spot. These processes frequently contribute to variability and inefficiency, yet they rarely receive the same data-driven insights as automated systems.
LightGuide’s augmented reality (AR) work instruction platform provides manufacturers with the tools to capture, analyze, and act on data from manual processes, driving efficiency and consistency across operations.
Imagine being able to pinpoint exactly where bottlenecks or defects occur—and uncover the root causes behind them. Or ensuring operators adhere to standard operating procedures (SOPs) without constant oversight.
Keep reading to:
- Discover why manual process data is a critical component of manufacturing analytics
- Learn how to capture and use manual process data to drive higher efficiency, quality, and workforce productivity.
- See how LightGuide bridges the gap in manufacturing analytics by providing visibility into manual process data.
IN THIS ARTICLE
The Critical Role of Manual Process Data in Manufacturing Analytics
How to Unlock Insights from Manual Process Data to Optimize Operations
Challenges of Incorporating Manual Process Data into Manufacturing Analytics
Best Practices for Leveraging Manual Process Data
Transforming Manual Process Data with LightGuide
The Critical Role of Manual Process Data in Manufacturing Analytics
While automated systems generate vast amounts of data for manufacturing analytics platforms, they only tell part of the story. Manual workflows often remain a black box, leaving critical inefficiencies unaddressed.
According to research from Kearney, 72% of factory tasks are performed by humans. Yet, these processes frequently remain unmonitored and unanalyzed, creating blind spots that impact efficiency and quality.
Without data from manual workflows, manufacturers risk missing opportunities to:
- Identify and eliminate bottlenecks.
- Reduce defect rates and improve quality.
- Standardize workflows and create consistency across shifts.
By leveraging tools like LightGuide, manufacturers can capture and analyze data from manual processes to bridge this critical gap in manufacturing analytics.
How to Unlock Insights from Manual Process Data to Optimize Manufacturing Operations
Manual process data is crucial to manufacturing analytics, providing visibility into variability and inefficiency issues that disrupt production. With LightGuide, manufacturers can automate the collection of manual process data through AR-guided workflows and empower teams to answer critical operational questions, such as:
- Where are manual tasks slowing down production, and why?
- What are the most time-consuming or error-prone steps, and how can they be redesigned to improve quality and throughput?
- Are there variations in execution across shifts or teams?
- How does adherence to SOPs correlate with defect rates and cycle times? Where are the largest gaps?
- Are workstation layouts contributing to inefficiencies or ergonomic challenges that impact worker productivity?
- Are training programs effective in ensuring SOP compliance and minimizing variability?
By tracking and analyzing data from manual workflows, manufacturers can:
- Detect and resolve defects at the source through root cause analysis, reducing rework and scrap.
- Optimize task sequences and workstation layouts to improve efficiency
- Standardize workflows and improve SOP adherence across shifts and locations
- Reduce variability that impacts quality and productivity
Here are six ways manufacturers can use manual process data to optimize operations:
1. Identify Bottlenecks and Increase Productivity
Manual workflows often contain hidden issues that can disrupt production flow. Capturing data from these workflows can help manufacturers identify bottlenecks, streamline processes, and increase throughput.
Tracking step and cycle times can reveal tasks that consistently exceed standard times, highlighting bottlenecks and opportunities to optimize task sequences. At the workstation level, operators can use tools like LightGuide’s Data Hub to monitor these metrics in real time, enabling them to adjust pace accordingly. Meanwhile, line supervisors can gain visibility into performance trends across workstations.
The impact: Identify bottlenecks, optimize production flow, reduce cycle time, and increase throughput.
Case study: Learn how L3Harris eliminated assembly-related defects and changeover per variant by using LightGuide’s projected AR work instructions for guidance and confirmation on high-variation lines. Read the full case study here.
2. Reduce Defects and Improve Quality
Manual workflows are often prone to errors caused by missed steps or deviations from SOPs. This variability makes standardization challenging. Tracking each task in real time can help enforce SOPs, reduce variability, and ensure consistency across shifts.
For example, LightGuide’s AR work instructions can flag skipped steps in real time, allowing operators to correct mistakes and prevent defective parts from moving downstream. Data-driven insights also ensure that quality-sensitive tasks—such as assembly, inspection, and testing—consistently meet required standards, transforming quality assurance from reactive to proactive.
The impact: Detect errors at the source, proactively reduce defects, and minimize costly rework.
Case Study: Using AR work instructions, this manufacturer reduced errors in hydraulic hose systems from 769 defect parts per million to zero, saving OEMs millions in FTC calculations for final assembly. Learn how, here.
3. Standardize Workflows Across Shifts and Locations
Variability in manual workflows, particularly across shifts or locations, is another common challenge that leads to inconsistent performance and quality. Without standardized processes, ensuring repeatable outcomes becomes difficult. By analyzing data from manual workflows, manufacturers can identify inconsistencies in task execution and enforce standardization across shifts and locations.
For example, tracking cycle times, defect rates, and process adherence can highlight deviations between shifts. These insights enable targeted retraining or process adjustments to ensure consistency, particularly in high-mix or multi-shift environments.
The impact: Enforce SOPs, reduce variability, and improve quality.
Case study: After implementing LightGuide on a production line with four workstations and nearly 100 parts bins, this transmission supplier eliminated process confusion, reducing cycle time dramatically and improving quality by 100%. Find out how, here.
4. Improve Workforce Performance
While manufacturing analytics often provide leaders with a system-wide view of operations, many organizations overlook a critical opportunity: empowering operators with real-time data at the point of work.
Traditionally, workers have depended on supervisors or engineers to identify and implement process improvements. However, access to real-time feedback enabled by data allows operators to self-correct and address inefficiencies directly at the source. For example, projected AR work instructions can guide operators through complex tasks step-by-step, ensuring efficiency and accuracy.
According to the Manufacturing Leadership Council, AR technology has the power to boost frontline worker productivity by as much as 50% and reduce human errors by up to 90%, making it an invaluable tool for manufacturers.
The impact: Empower decision-making and problem-solving on the factory floor to enhance productivity, accountability, and continuous improvement.
5. Improve Training
Manual process data also plays a critical role in improving training effectiveness. By capturing and analyzing manual workflow data as part of broader manufacturing analytics strategies, companies can:
- Identify skill gaps: Metrics such as task completion times and error rates help identify areas where workers may benefit from additional training.
- Enhance training effectiveness: Insights into performance trends allow organizations to design training programs that proactively address common challenges.
- Accelerate learning curves: AR guidance enhances on-the-job training by providing real-time feedback. This shortens ramp-up times for new or reassigned employees, enabling them to achieve productivity goals faster.
According to research from the World Economic Forum, businesses have reported that AR training effectiveness improved by as much as 80% when compared to traditional methods.
The impact: improve workforce readiness and accelerate upskilling while reducing the time and cost associated with traditional training methods.
Case Study: Using AR work instructions, this EV innovator optimized training and assembly workflows to achieve breakthroughs in quality and productivity, including a 50% decrease in cycle time and a 75% decrease in training time. Discover how here.
6. Smarter Resource Allocation & Decision-Making
Every decision on the factory floor—from optimizing production schedules to improving quality—depends on clean, actionable data. Without this information, manufacturers miss opportunities to optimize manual processes—whether it entails improving workstation layouts, refining task sequences, or tackling variability at its source.
By capturing manual process data as part of broader manufacturing analytics strategies, companies can better align labor, equipment, and materials with production demands—reducing waste and maximizing output.
The impact: Smarter staffing decisions, optimized resource allocation, minimized downtime, and better operational efficiency.
RELATED ARTICLE: 6 Uses of Augmented Reality for Manufacturing in Every Industry
Challenges of Incorporating Manual Process Data into Manufacturing Analytics
While the benefits of manual process data are clear, implementing these strategies as part of broader manufacturing analytics initiatives isn’t without challenges. However, with the right tools, organizations can overcome these hurdles and transform manual workflows from an operational blind spot into a competitive edge.
1. Visibility Gaps in Manufacturing Analytics
Unlike automated systems, manual workflows often lack the tools and infrastructure needed for real-time analytics, leading to gaps in visibility and missed opportunities for improvement. As a result, hidden issues can ripple across operations, causing missed production targets, increased defect rates, and wasted resources.
If manual processes are tracked at all, it’s often done post-facto, meaning inefficiencies or errors are only identified after they’ve disrupted production. Without visibility into manual processes, manufacturers are left guessing where inefficiencies occur or why defects happen, limiting their ability to take timely and corrective action.
For example, a plant manager might struggle to identify why a specific shift consistently misses production targets. Without data from manual workflows, the root cause remains unclear, preventing intervention and further compounding issues. LightGuide’s AR work instructions eliminate this guesswork, enabling manufacturers to take corrective action where it matters most.
2. Growing Complexity Across Disconnected Systems
Manufacturing environments often involve a mix of legacy systems, modern automation, and manual processes. This complexity often results in disconnected systems and data silos that inhibit the seamless flow of information across operations.
These challenges are particularly pronounced in manual workflows. Unlike automated processes, which often benefit from built-in connectivity and analytics, manual workflows frequently operate in isolation. Without integrated tools or frameworks, incorporating data from manual workflows into broader manufacturing analytics platforms can be a complex and resource-intensive process.
Bridging this gap is essential, as true operational intelligence requires a unified approach to data management. For instance, LightGuide makes it possible to connect manual process data with other manufacturing analytics platforms, enabling manufacturers to gain a more complete understanding of operations.
3. Data Accuracy & Cleanliness
Clean, reliable data is essential for making informed decisions, but capturing accurate information from manual workflows remains a persistent obstacle. Unlike machines that continuously generate structured logs, manual processes rely heavily on human observation and input, which are inherently prone to error.
Compounding this challenge is the sheer volume of data generated on the factory floor. Manual workflows produce significant data, including step times, cycle times, takt times, error rates, and more. Without a structured system to organize, prioritize, and analyze this information, manufacturers risk becoming overwhelmed—losing key insights in a sea of noise.
For instance, an industrial engineer conducting a production time study might encounter several obstacles. A missing timestamp, inaccurate entry, or inconsistent reporting methods across shifts could distort analysis. This can lead to suboptimal decisions about workflow optimizations or missed opportunities to improve training programs.
Standardized data capture and validation tools are critical for clean, reliable data. LightGuide minimizes reliance on manual data entry by automatically capturing and organizing key performance metrics while detecting anomalies for reliable data modeling.
Best Practices for Leveraging Manual Process Data as Part of Manufacturing Analytics
By following best practices for capturing and analyzing manual process data, manufacturers can transform these challenges into opportunities for improvement.
1. Focus On High-Impact Areas
Start by targeting workflows that impact quality, efficiency, or consistency, such as assembly, inspection, or material handling. Manual workflows with frequent variability or errors are prime candidates for optimization. This way, teams can pinpoint inefficiencies and redesign workflows to ensure repeatable outcomes.
2. Digitize Manual Workflows
Digitizing manual workflows with tools like AR work instructions allows companies to capture manufacturing data and analytics as tasks are performed, gaining visibility into key metrics such as step times, cycle times, defect rates, and more. These metrics, along with operator IDs and part identifiers like barcodes, enable full digital traceability of manual workflows.
By collecting this data, manufacturers can gain insights into performance trends across workstations and work cells. This includes understanding team performance across shifts or locations, enabling organizations to identify inefficiencies, standardize processes, and optimize productivity on a larger scale.
RELATED ARTICLE: Digital Work Instructions Explained: The Ultimate Guide
3. Empower Front Line Workers with Real-Time Feedback and Data
For years, the conversation around manufacturing analytics has focused on enterprise-level dashboards and system-wide insights. While these tools are invaluable for leadership and strategic planning, they often leave a critical group out of the equation: the workers on the factory floor.
These individuals are closest to the process yet often lack access to insights that could help them excel. Empowering them with AR guidance and real-time data is a game-changing strategy that enables them to take ownership of their performance and achieve higher efficiency, quality, and productivity.
When workers are equipped with real-time data at their workstations, the results are transformative.
- Faster process improvement: Real-time performance metrics provide operators with immediate feedback, enabling them to self-correct and optimize performance on the spot.
- Better process adherence: AR work instructions can provide step-by-step guidance and flag deviations in real time, improving efficiency and eliminating errors. Paired with 3D sensors and machine vision, LightGuide’s AR platform verifies part placement and alerts operators to deviations, enabling immediate corrections before impacting downstream processes.
- Higher workforce productivity: Access to performance metrics empowers workers to meet and exceed goals, fostering accountability and continuous improvement.
- Faster training: Real-time feedback provided by tools like AR accelerates the learning curve for new employees, allowing them to achieve proficiency faster.
This worker-centric approach to manufacturing analytics bridges the gap between manual processes and data-driven strategies, ensuring operators play an active role in enhancing production outcomes.
RELATED ARTICLE: The Digitally Connected Worker
4. Iterate and Improve
Data from manual manufacturing processes lays the groundwork for continuous improvement. Real-time insights at the workstation empower operators to self-correct, while aggregated data enables supervisors to identify trends, address inefficiencies, and prioritize process improvements. By establishing a real-time feedback loop, manual process data complements automated data strategies.
These challenges highlight the need for innovative solutions to bring manual workflows into the fold of modern manufacturing analytics. As noted by Forbes, AR is not only part of the next generation of Industry 4.0, it is changing manufacturing entirely. By bridging gaps in visibility and empowering workers, AR enables manufacturers to modernize operations and stay competitive in an increasingly data-driven industry.
Transforming Manufacturing Analytics with Manual Process Data from LightGuide
While automated systems are equipped with sensors and advanced analytics, manual workflows remain unmonitored, unanalyzed, and unoptimized. LightGuide bridges this gap by integrating AR-guided workflows with data capture and analysis, empowering manufacturers to transform blind spots into actionable insights. From enhancing operator performance with real-time feedback to connecting manual processes with enterprise systems, LightGuide enables organizations to unlock the full potential of their data.
Enterprise Connectivity for Unified Manufacturing Analytics
LightGuide’s versatile platform bridges the gap between manual workflows and data-driven decision-making. Its capabilities extend beyond data capture, enabling manufacturers to ingest information from their MES or other enterprise systems, export manual process data for integration into broader manufacturing analytics platforms, and provide real-time insights directly to operators at the workstation.
Delivering Real-Time Insights Where They Matter Most
While LightGuide integrates with enterprise systems and manufacturing analytics platforms to unify operational data, its Data Hub feature shifts the focus from top-down analytics to workforce empowerment. Designed with operators in mind, it delivers real-time insights to the people closest to the process and drives improvements where they matter most: on the factory floor.
With LightGuide, data-driven insights become part of the workflow itself. A library of pre-built queries simplifies access to key metrics like cycle times, rework rates, and user performance, and makes manual processes smarter by allowing workflows to adjust based on performance data. Additionally, these queries can seamlessly share data through a database, fostering better integration with existing manufacturing analytics systems.
Feedback Loop for Continuous Improvement
By uniting manufacturing analytics and workforce engagement, LightGuide creates a dynamic feedback loop that fuels continuous improvement. Operators receive real-time guidance to optimize performance, while supervisors leverage data to refine processes and address inefficiencies. This dual focus empowers teams to make informed decisions, refine workflows, and drive measurable improvements.
Key Features & Benefits of LightGuide’s Data Hub
- Real-time tracking and traceability: Gain full digital traceability by tracking and logging every step of a manual process in real time.
- Gamification of work: Enhance the operator experience by gamifying work. Operators can track key metrics directly at their workstations. This not only improves engagement but empowers them to make immediate adjustments.
- Greater visibility for line supervisors: Step times, cycle times, and quality data enable supervisors to monitor workforce productivity, coach employees more effectively, and make targeted process adjustments to improve overall performance.
- Advanced data tools for greater operational intelligence: With pre-built queries, customizable dashboards, and anomaly detection, LightGuide empowers teams to maintain data integrity with reliable data modeling.
A Holistic Manufacturing Analytics Strategy Built for the Future
In today’s competitive manufacturing landscape, data drives smarter decisions, higher efficiency, and consistent quality. Yet, manual workflows often remain overlooked, leaving significant gaps in visibility and missed opportunities for optimization.
Addressing these blind spots is critical for unlocking the full potential of your operation. By integrating manual process data into broader manufacturing analytics strategies, companies can reduce variability, optimize productivity, and enhance quality.
With tools like LightGuide’s AR work instruction platform, manual workflows become a source of actionable insights and measurable improvements—empowering operators to improve performance and providing leaders with the visibility needed to drive continuous improvement.
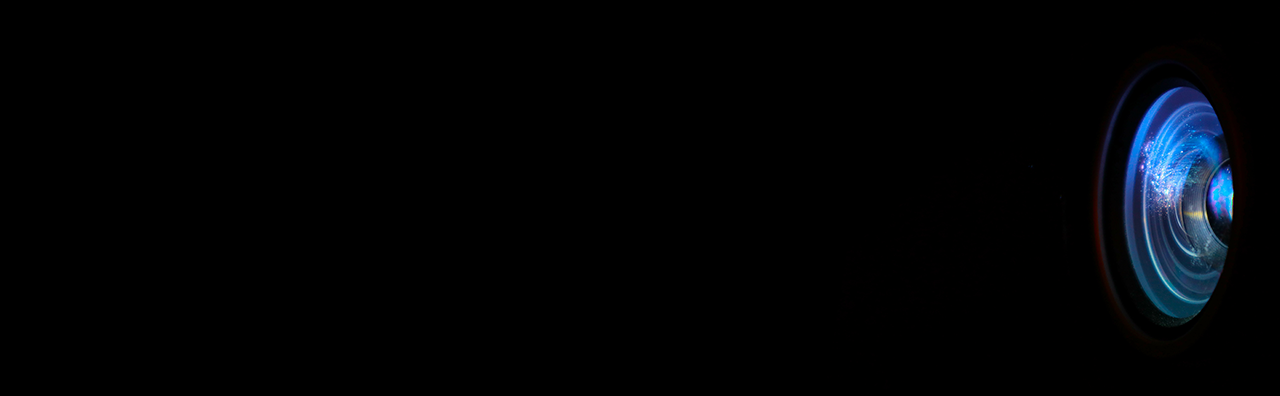
Ready to Unlock the Full Power of Your Data?
Contact us today to explore LightGuide’s AR platform.