Quality and throughput have always guided manufacturer’s decisions to invest in new processes and technology. With the influx of interactive Industry 4.0 technology, manufacturing leaders are presented with many choices—like 3D printing, artificial intelligence, and augmented reality.
Augmented reality (AR) is gaining popularity across a wide variety of industries and applications, such as automotive, aerospace, medical, and electronics. It exceeds operational needs and provides tangible benefits such as effective training and traceability.
There are three main types of augmented reality for manufacturing applications; tablet-based, wearable, and projected. Of the three, projected augmented reality delivers the most benefits, expanding past basic operational needs and changing the way we see manufacturing.
Projected Augmented Reality
Projected AR uses a combination of projectors and vision sensors to display step by step interactive graphics onto any work surface. Compared to tablet-based and wearable AR, the versatility of projected AR for manufacturing applications is more practical and precise. For over 10 years, projected AR has delivered proven results for leading manufacturers around the world. Often, return on investment is delivered in six months or less. It is usable across every industry for full-time guidance, error prevention and detection.
Benefits of Projection-Based AR
Projection-based AR bridges the gap between automation and human-centric production. By combining the best of human intelligence and technology, It brings out the best of Industry 4.0 to empower and retain workers while increasing productivity, throughput, and training effectiveness.
Designed to make factory floors smarter, safer, and more efficient, projector-based augmented reality uses advanced projection technology to overlay a virtual operating “canvas” onto any work surface and guides operators through a series of audio and visual prompts.
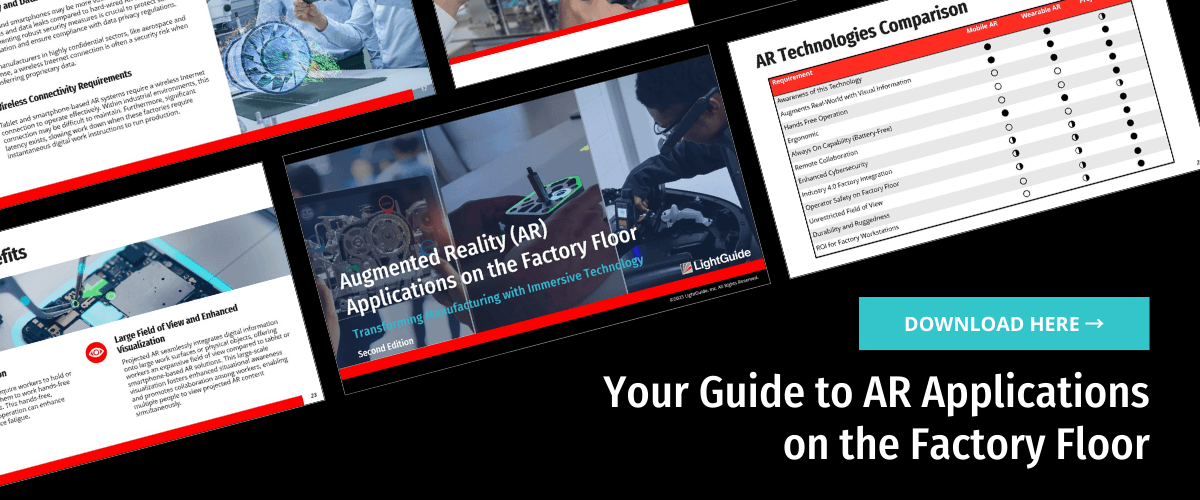
Because projected AR guides workers to simply “follow the lights,” training time is dramatically reduced and workers become productive much faster as a result. It’s so intuitive that nearly anyone can walk up to a station and complete the work with no prior knowledge. This applies to individual or group training, as systems are scaled to fit individual or multi-operator work areas.
In addition, the added sensory engagement through audio and visual prompts increases training retention and aids the growth of an adept agile workforce while also providing a natural “layered audit” process for manufacturing through its “See What I See” technology.
First, when discussing visuals, the Visual Teaching Alliance found that “approximately 65% of the population are visual learners” and that “the brain processes visual information 60,000 faster than text.” So, it’s no surprise that visuals make training more engaging. Videos and animations also promote gamification and a level of interaction that isn’t as high in tablets or wearables.
Secondly, many people with disabilities find it easier to comprehend visual and auditory information. ReadingRockets.org proves this in their research, which found that students understand more material presented through visuals. Graphics and sounds draw more attention to actions and simplify steps. Therefore, using visuals lowers the cognitive load and makes it easier to react. These features are inclusive to those without cognitive barriers too. People with language barriers operate with less text, and people with color blindness are aided by specific color ranges available only in projected AR.
Between graphics, videos, text, and audio prompts (among many other indicators), the right information is displayed in the right place and at the right time. What is meant by that is the right information (the precise work instructions for the process) are where they are needed (directly in front of the worker and on the operation) and appear exactly when they are needed (they only see one step at a time). Therefore, the instructions are concise, keep workers’ eyes on their operation, and focus on the quality of each action. All of these factors increase safety, cognitive capacity, and overall operational success.
Some factories attempt to test and simulate process designs with digital twin models. The digital twin illustrates what an operation would look like and how a worker should perform it. However, when these digital models are deployed on the factory floor, the models often do not meet the design goals. Projected AR creates a physical twin from the digital twin allowing actual processes to achieve the digital metrics as proven by real-time metrics possible from both manual and automated processes. The software captures real-time analytics such as OEE, torque values, and training time thereby tracking and measuring manual tasks.
Projected AR software is configurable to hundreds of standard factory tools, including MES, PLC, torque tools, cameras, and sensors. It allows for a complete look at processes and traceability to identify specific problems within the operation. It is also deployable on an enterprise level, easily interfacing with common cloud platforms to create custom dashboards and analytics. This includes analytics products such as Microsoft Power BI and Siemens MindSphere.
These analytics are easily accessed or restricted based on user status. Users with higher-level access can make changes as needed. Say procedures change by one bolt placement. The user can log in, then drag and drop graphics in minutes to adapt to the new process. Easy to use and program, projected augmented reality is a plug-and-play system that is quickly up and running.
One of the unique features of projected AR software is enhanced “no-faults forward” error prevention. Instead of only checking for errors in production at the end of a cycle, the software prevents errors by guiding workers throughout the process with confirmation for key steps that the work was correct. An example of this is correct tool measurement before moving forward to the next step. The software connects to smart tools and reads the measurements in real-time. Then, depending on proper step completion, a worker can move on or go back. Therefore, the work is accurate the first time.
Finally, projection-based AR hardware is extremely durable and flexible to run in 24/7 manufacturing operations without the need to charge batteries or rely on wireless connectivity. All projected AR hardware integrates within new or existing production cells and is easily re-deployable around the factory. It is resistant to tough manufacturing environments, making it ideal for even the most challenging applications.
Successful manufacturing processes are able to make every second and every penny count in their operations. Due to the wireless transfer of data, tablets and wearable headsets often have large latency and delays between when information is required and when it is available. In addition, they can be dropped and require consistent care, whereas projected AR delivers real-time work instruction and has minimal maintenance. There is nearly no risk of dropping or breaking the equipment, and it is very self-sufficient as it connects to factory electricity without the need for charging or battery swaps. The downtime that comes with tablets and wearable charging is non-existent. Projected AR is the only type of AR to run full-time, limiting manufacturing delays.
Projection-Based Trade-Offs
The main qualm with projection-based AR is that it is not a well-known technology. Therefore, manufacturers question its reliability. In actuality, projection-based AR provides the most realistic examples of its usability before purchase.
Whereas commercials for tablets and wearables show off apps and graphics that are edited to provide an idea of what is seen, projection-based AR shows the exact user experience. The projector functions in any environment to display visuals. Demonstrations of this technology mimic exact manufacturing scenarios.
Along with that, because projection-based AR is bolted into supports, there is no risk of a worker moving around and placing themselves into unsafe situations. Additionally, the workbench paired with the projector is often custom-built to meet ergonomic needs, so it provides extra safety measures for users.
Making Projected AR Work
Projection-based augmented reality is the only type of AR that provides undelayed, full-time operational guidance. It guides an extensive number of applications and an unlimited variation of products. Among its software and hardware benefits: intuitive, interactive instructions, physical twin models, placing the right information in the right place and at the right time, durability, scalability, and security; projected AR evolves operations off the work station as well.
Implementing systems that create more worker retention and inclusion enhance company cultures. More accommodating work creates more worker satisfaction. And, as the projected guidance alleviates stress, more time is spent thinking about the process. This new mindfulness can cause workers to think of new solutions and enhancements to operations. As work becomes meaningful, workers are more satisfied and engaged with their work. Together, these new perceptions increase the agility of the business, propelling it into the future.
Overall, projected augmented reality enhances processes and cultures across a wide variety of industries and applications. When considering investing in Industry 4.0 technology for manufacturing, projected augmented reality exceeds operational needs and transforms business.
To find out more about projected AR applications on the factory floor, contact our team or request a demo.