Hearing the word ergonomic, you might think of expensive computer chairs designed to eliminate back pain. And physical ergonomics is a large contributor to the work environment. However, ergonomics as a whole is entirely more complex and has applications in a variety of industries, including manufacturing. In this article, we’ll explore ergonomics, its three forms, and how to apply it across your organization.
What is Ergonomics?
Ergonomics is “an applied science concerned with designing and arranging things people use so that the people and things interact most efficiently and safely;” defined by Merriam-Webster.
Above all, manufacturers aim for a highly efficient and safe work environment. Therefore, it stands to reason that ergonomics is critical to the success of an organization. But what is the best way to implement ergonomics in a manufacturing environment?
Types of Ergonomics
Before buying hundreds of new chairs, it’s important to develop an understanding of how ergonomics affects people. There are three types of ergonomics: physical, cognitive, and organizational. Each of these differently affects how people interact with their environment, contributing to how effective they are in their work. Ultimately, each type of ergonomics contributes not only to organizational success but also to worker satisfaction and the bottom line.
Physical Ergonomics
Physical ergonomics is the most commonly known form of ergonomics, and for good reason. It deals with the physical load on the human body when performing activities. Understanding physical ergonomics and how to integrate it heavily influences on-site safety.
Usually, if physical ergonomics is disregarded, workers can develop musculoskeletal disorders (MSDs). OSHA notes that MSDs “affect the muscles, nerves, blood vessels, ligaments and tendons… which can increase a worker’s risk of injury.” In 2018, the Bureau of Labor Statistics found that 30% of all manufacturing worker injury and illness cases resulted from MSDs.
Awkward body positioning, reaching overhead, and consistently repeating similar tasks are a few of the activities that OSHA identifies as causes of MSDs.
As work instructions are designed, it is important to limit these risks by understanding who will be using the instructions. The Ergonomic Systems Associates (ESA) identified some of the different needs for workstation construction based on the worker’s specific needs and the materials or items they are working on.
For example, the weight of a material or item that a manufacturer works on can affect ergonomics as well as the height of the worker. Regardless of the task being performed, someone who is 5’2” will not be able to work comfortably at a table set for someone who is 5’9” tall.
Acquiring workstations that are height adjusting, like LightGuide’s smartAR workstation, can be an easy way to ensure that multiple workers can use the same station. Then, you don’t have to spend money to buy multiple types of stations or assign workers to certain areas based on their body type.
![]() |
![]() |
Explore the LightGuide smartAR™ Workstation
The following image shows how high a standing workstation should be based on the weight of the material or item being worked on.
Cognitive Ergonomics
Cognitive ergonomics is the method of designing and arranging information and data to create a light cognitive load.
Perception, memory, reasoning, and motor response all affect how someone interacts with and performs their work. A higher cognitive workload causes more stress on the worker.
Paper work instructions are one example of increased cognitive workload, as they require memorization and focus. A worker has to look from the paper to their work; cognitively connect the written steps to the movements needed, complete the task, and then ensure that it was correct. Even though it only takes milliseconds for your brain to make those decisions and react, compared to visual work instructions, a worker has a larger cognitive load.
Simplified work instructions that place the right information in the right place and at the right time lessen cognitive load.
Projected augmented reality work instructions, for example, break steps down into digestible bits of information. The step instruction is overlaid onto the part, requiring no memorization. Then, during the work, projected work instructions can direct workers to the exact needs of the task (say, aligning a part to a precise position). Finally, audible and visual confirmations ensure quality and completion.
Visual work instructions also open more opportunities for workers with cognitive disabilities or general difficulty completing tasks to more easily engage with their work.
Overall, workers do not need to focus on the instructions steps and can move their focus to safety, continuous improvement efforts, quality, or simply finishing the task. Learn more about LightGuide projected AR work instructions here and by viewing the video below:
Organizational Ergonomics
Organizational ergonomics combines the knowledge gained from other areas of the factory, like physical and cognitive ergonomics, to optimize safety and efficiency across the entire organization.
Business Wire explained that “this entails finding ways to optimize teamwork, improve communications, increase output and bolster the overall quality of a product. This can show itself in many ways; standardized training, unified data storage through the cloud, or lean manufacturing techniques.
For example, operators are often the best resource for understanding a process and making it more efficient. By including them in a digital transformation plan, you can unify communications and standardize processes. Not only are you capturing tribal knowledge, including them will improve their adoption and engagement of new technologies.
Applying Ergonomics Throughout An Enterprise
To enable ergonomics within a factory, manufacturers should invest in technologies that encompass multiple, if not all, forms. Proven Industry 4.0 technologies like projected augmented reality are an all-in-one ergonomic option that easily deploys around the factory.
Projected augmented reality applies the best practices of all forms of ergonomics. It integrates with the latest assistive technology to increase physical ergonomics—seamlessly connecting to cobots, ProGloves, or providing instructions on height-adjusting tabletops on the LightGuide smartAR workstationTM. It lowers cognitive load by delivering immersive visual instructions, putting the right information in the right place, at the right time. By decreasing memorization and unnecessary movements, projected augmented reality increases productivity and efficiency, benefitting the organization and the worker. Overall, enabling physical and cognitive ergonomics enables organizational ergonomics, optimizing output, quality, and communications by tracking manual data.
Fully Optimizing Efficiency and Safety
Ergonomics is more than just a way to relieve back pain. Understanding the three different types provides greater insight into the complex work environment of the modern, mature factory floor.
Leading manufacturers are prioritizing ergonomics and rearranging their workplace and their relationships with their workers. By doing this, they gain increased worker satisfaction, quality, and efficiency. Ultimately, manufacturers achieve a greater bottom line.
AR Solutions to Enhance Ergonomics
LightGuide projected AR solutions can improve ergonomics in the workplace, helping to improve productivity, and create a safer and more comfortable work environment.
eBook | Augmented Reality (AR) Applications on the Factory Floor
Download the eBook to Discover:
- 3 types of AR manufacturers are using today
- The benefits and limitations of each
- Comparison chart to match AR to your factory application
- Real-world case studies of industrial AR
- How to use AR to scale, optimize, and empower your factory
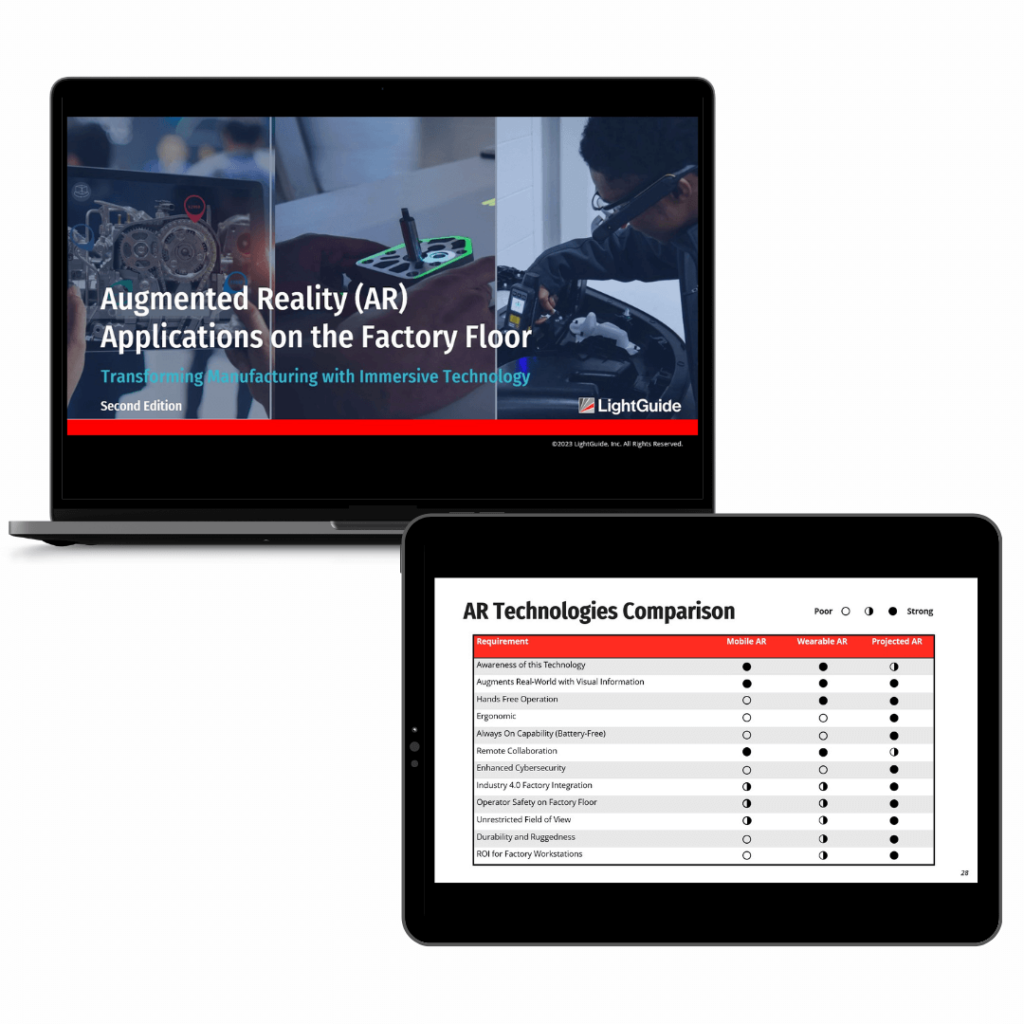
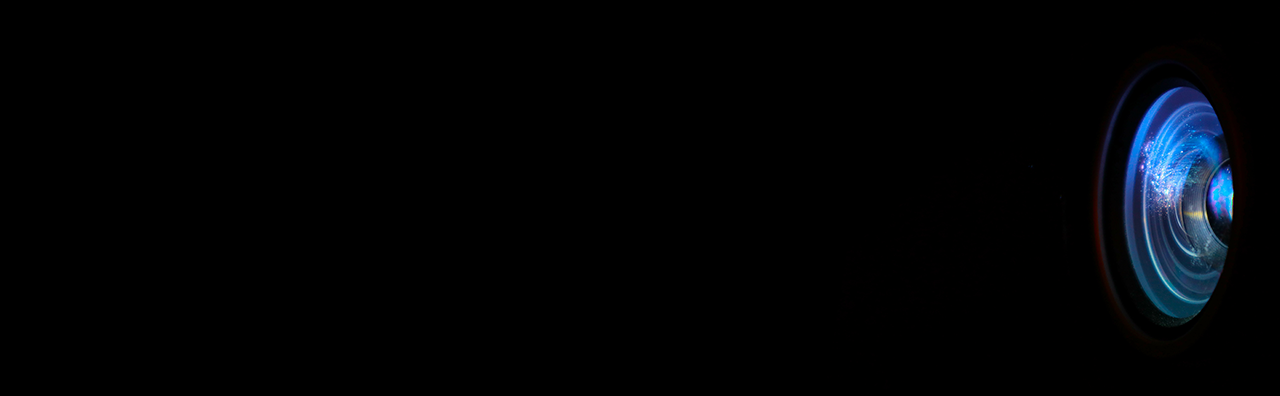
Ready to Explore How Projected AR Work Instructions Can Give Your Workforce a Competitive Advantage?
Connect with our team to see how the LightGuide platform can transform your operations.